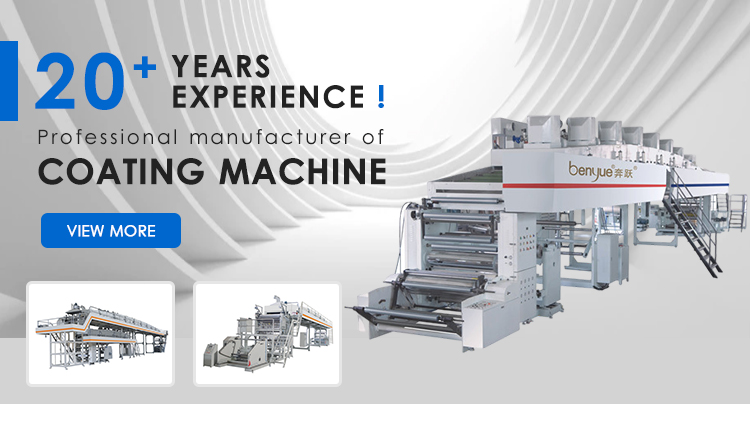

Type
|
Wet laminating machine
|
Work effective width
|
1300mm
|
Machine max line speed
|
150m/min
|
Laminating max. line speed
|
120m/min
|
Guide wheel width, diameter
|
φ100mm×1350mm
|
Rewinding and unwinding type
|
Double station, fully automatic material receiving
|
Heating method
|
electric heating
|
Oven lenght
|
12m
|
Electrical power
|
96KW
|
Overall machine motor power
|
68KW
|
Dimension (L*W*H)
|
14500×3100×4300mm
|
machine weight
|
16000kg
|
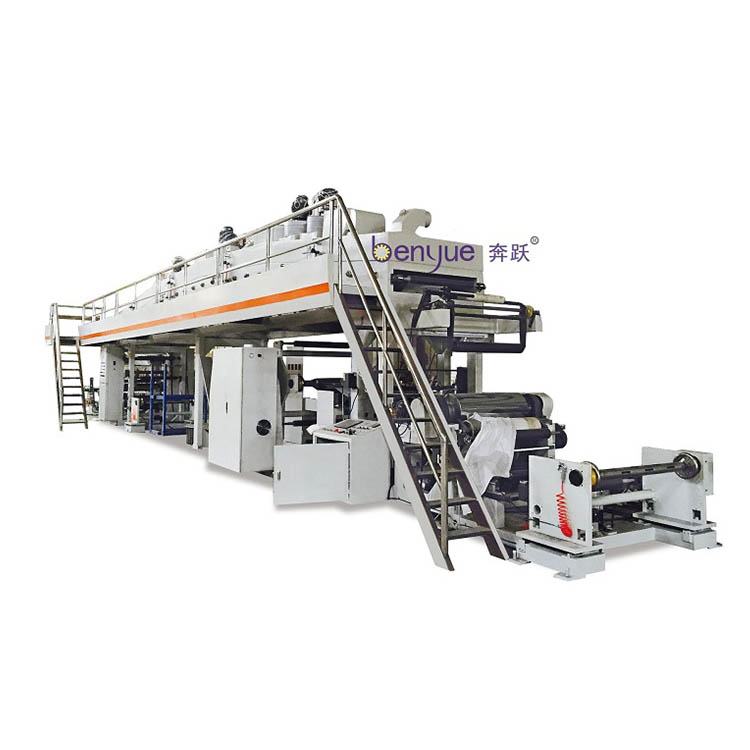
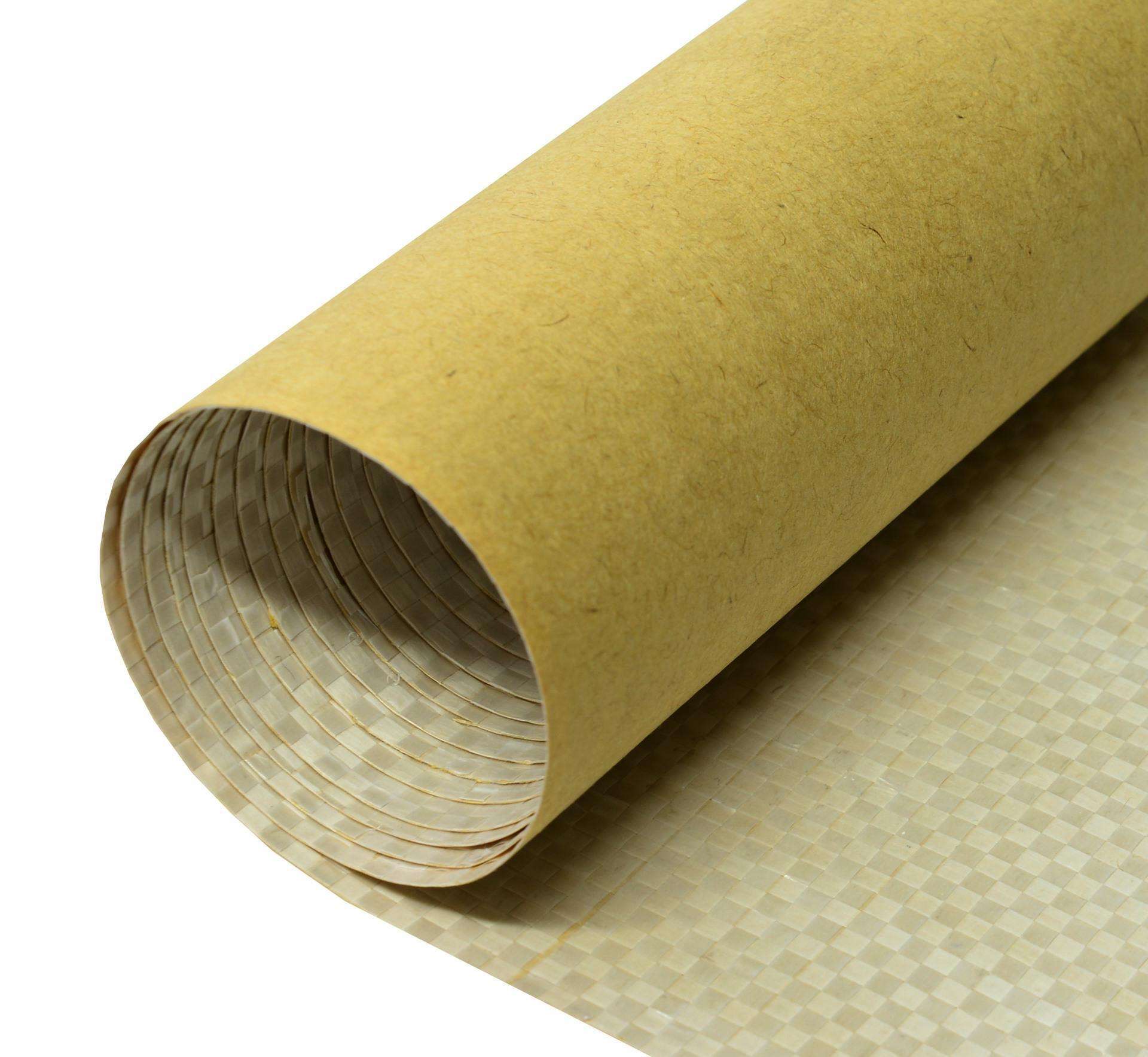

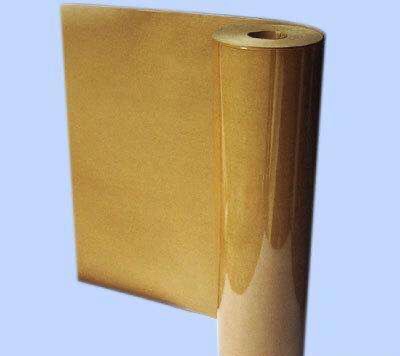
1. The whole machine adopts imported PLC for logic tension control and protection to improve the reliability of the whole machine
2. The four closed-loop constant temperature tension of unwinding, glue coating, compound traction and winding is controlled and displayed through the man-machine interface
3. The gluing method is anilox coating. The coating scraper shaft adopts heavy-duty double shaft mechanical independent swimming. The scraper adjustment method is manual with pneumatic, and the angle can be adjusted arbitrarily. The coating amount depends on the mesh line of the anilox roller. The anilox roller with different mesh line can be changed for different coating amount
4. Four stage air top constant temperature oven with stratified inlet and outlet air, negative pressure design, strong wind force, complete drying and secondary return air, which not only saves energy, but also reduces the content of residual solvent 5. The guide roller in the oven adopts active and passive type, and the transmission adopts synchronous pulley transmission type to reduce material tension and deformation
6. the first, second and third unwinding (mask and bottom film) are corrected by EPC. EPC oblique rectification is also adopted after the film is out of the oven
7. High precision anilox roll coating system, pneumatic scraper, uniform roll and glue circulation device
8. High precision back pressure three roll composite device. The composite roll adopts sandwich heat transfer oil circulation and intermediate electric heating tube heating to make the composite more uniform and older
9. The coating and compounding unit adopts double frequency conversion linkage drive and enters PLC computer program control
10. Make the composite film smoother and scratched by cooling roller
11. Two sets of AC vector motors are used in the winding part, which are controlled by PLC computer system. The pneumatic back pressure roll cutter cuts and automatically winds up to reduce loss
12. The retracting and releasing shaft adopts the expander type inflatable shaft, which is convenient for loading and unloading
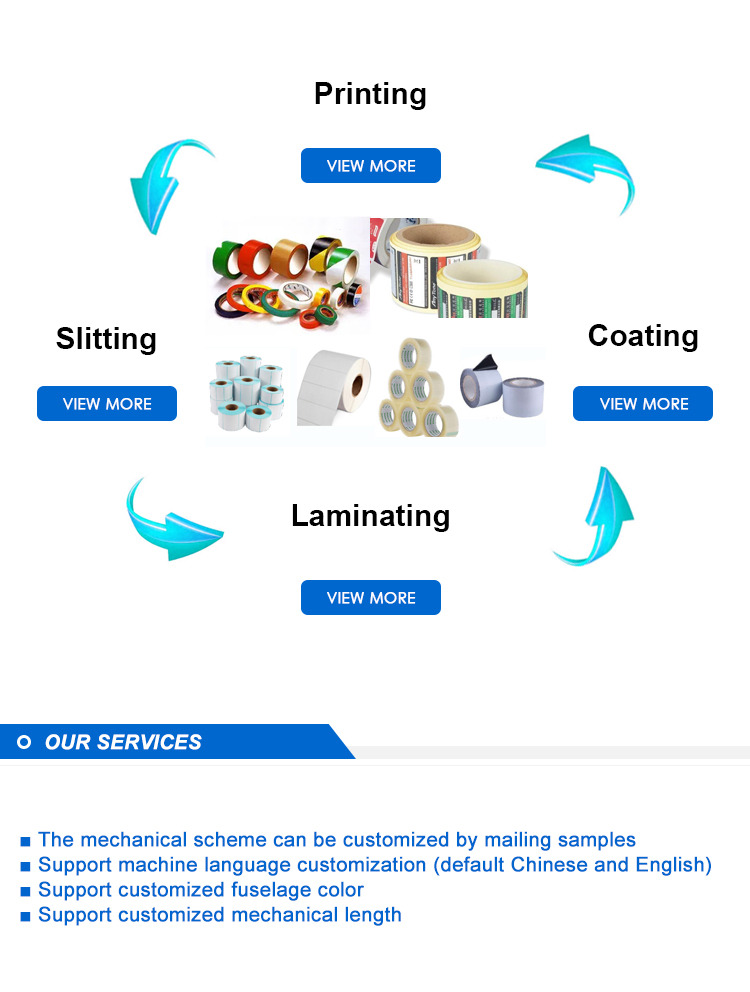
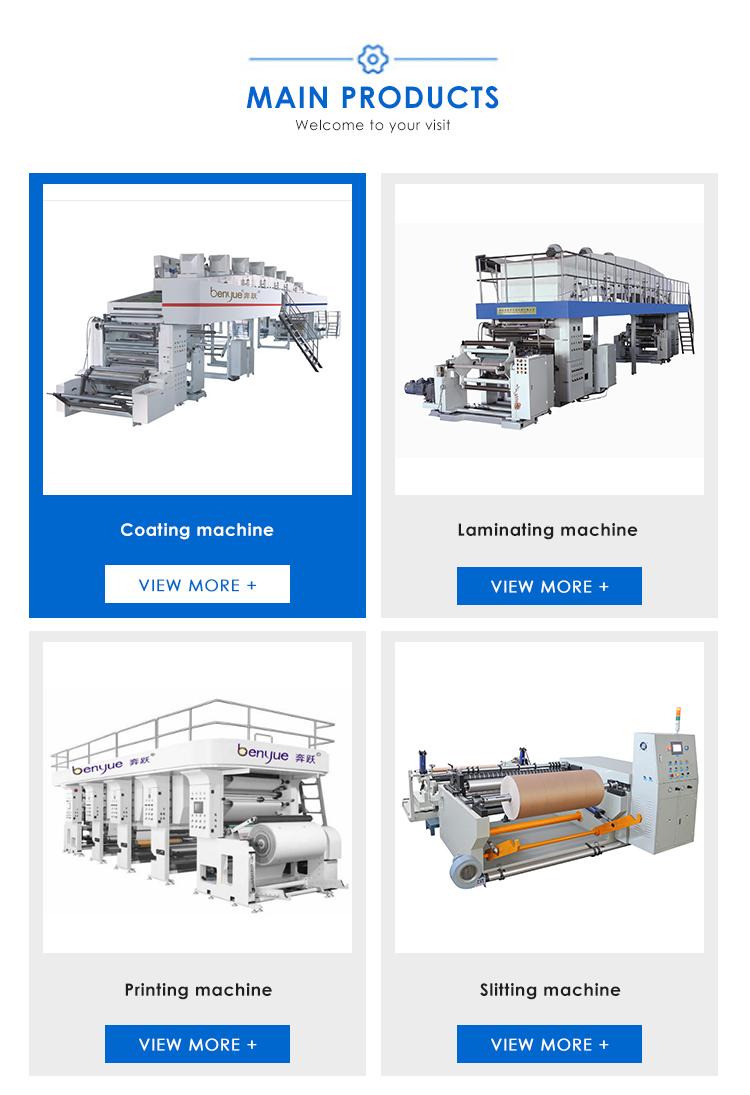
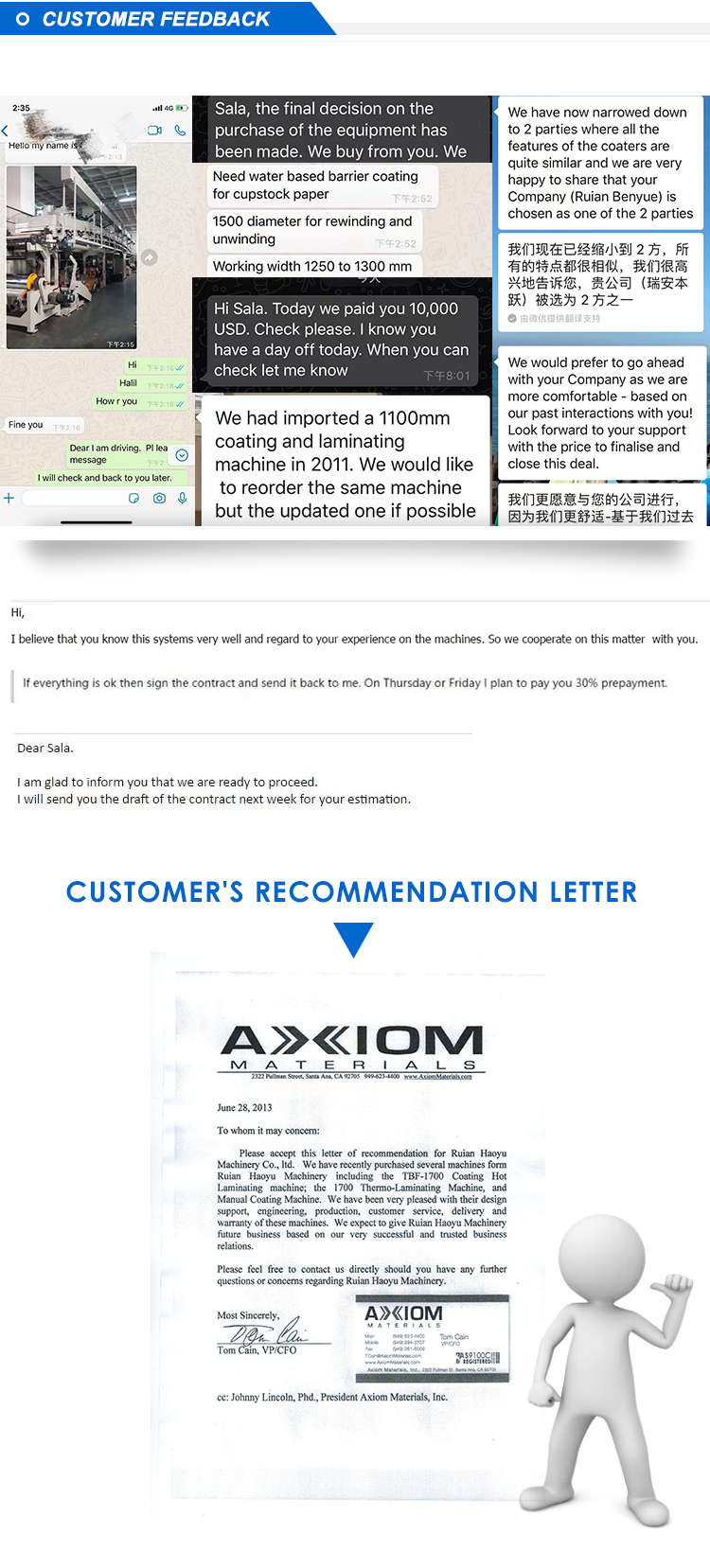
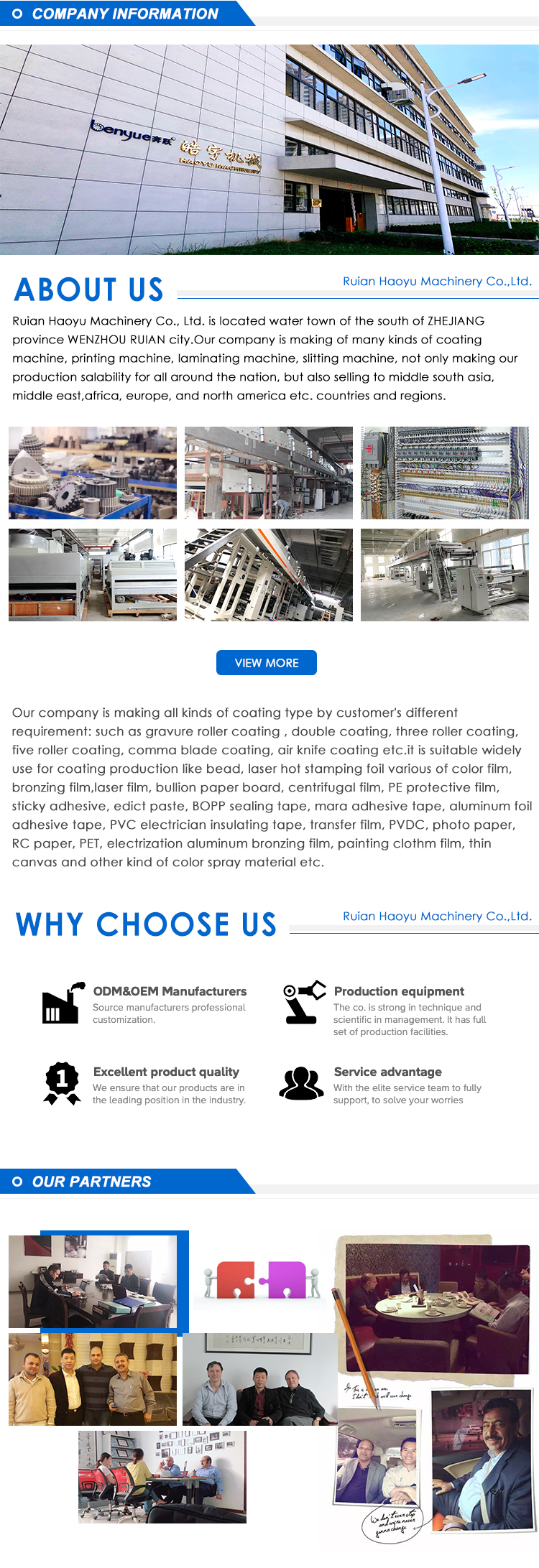
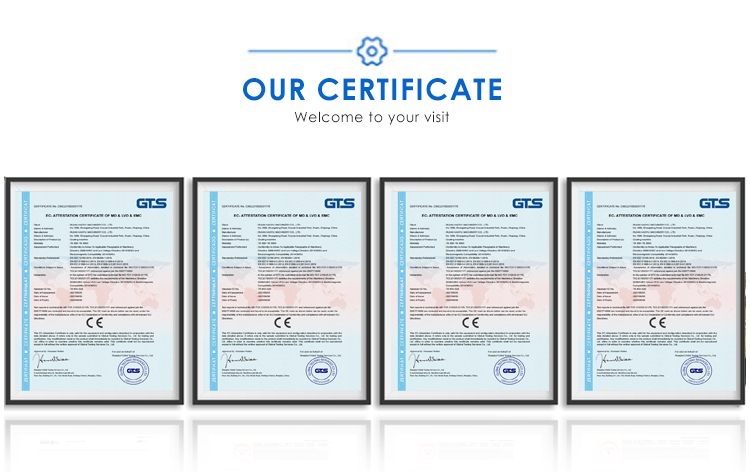
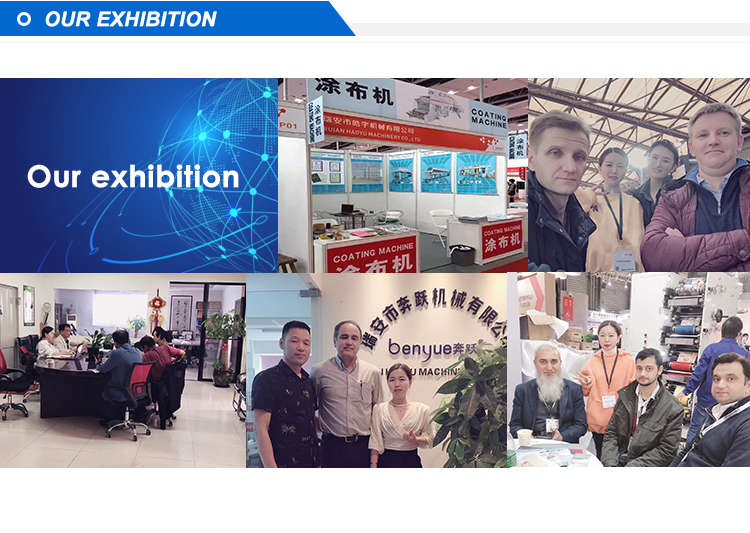
