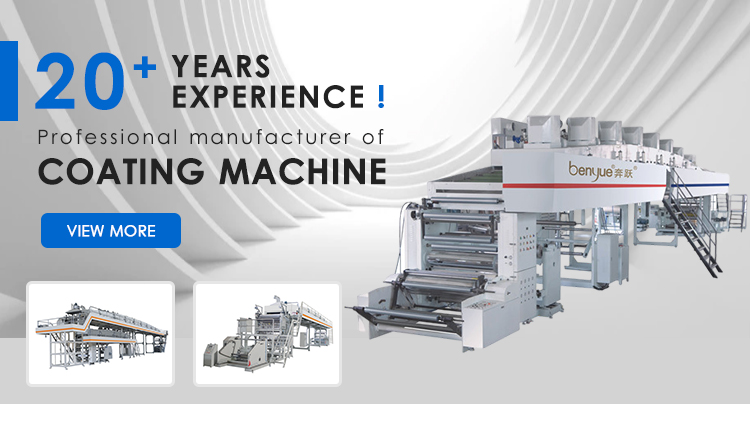

Model
|
TB600-2500 mesh fibric adhesive tape coating machine
|
Coating method
|
comma blade coating / gravure roller coating/ mayer bar coating /air knife coating / five roller coating / blade coating / slot die coating /micro gravure coating (Can be customized)
|
Coating width
|
600-2500MM (Can be customized)
|
Unwinding diameter
|
600-1500MM (Can be customized)
|
Winding diameter
|
600-1500MM (Can be customized)
|
Coating thickness
|
2-300g/square meter
|
Coating speed
|
10-300m / min (depending on material)
|
Heating method
|
Electric heating, oil heating and natural gas heating
|

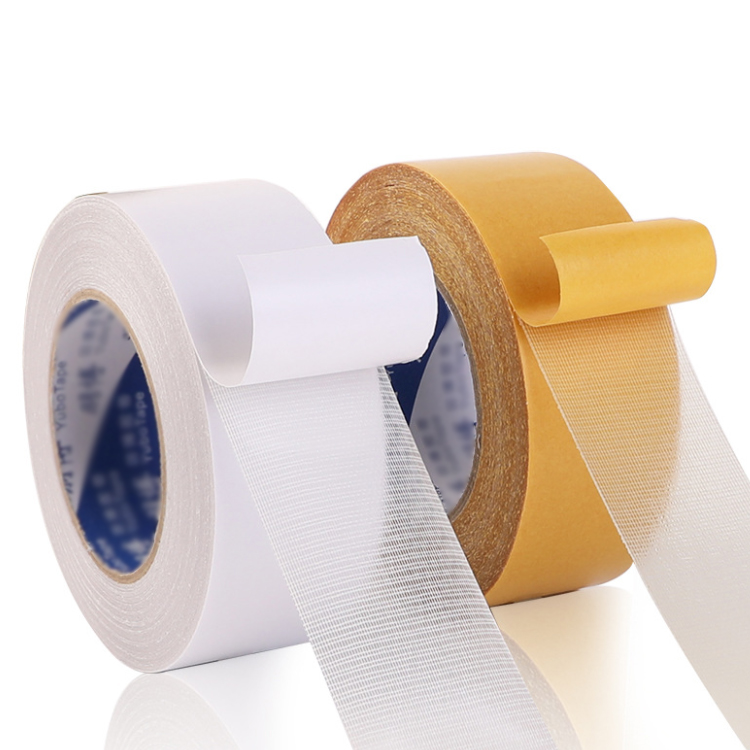
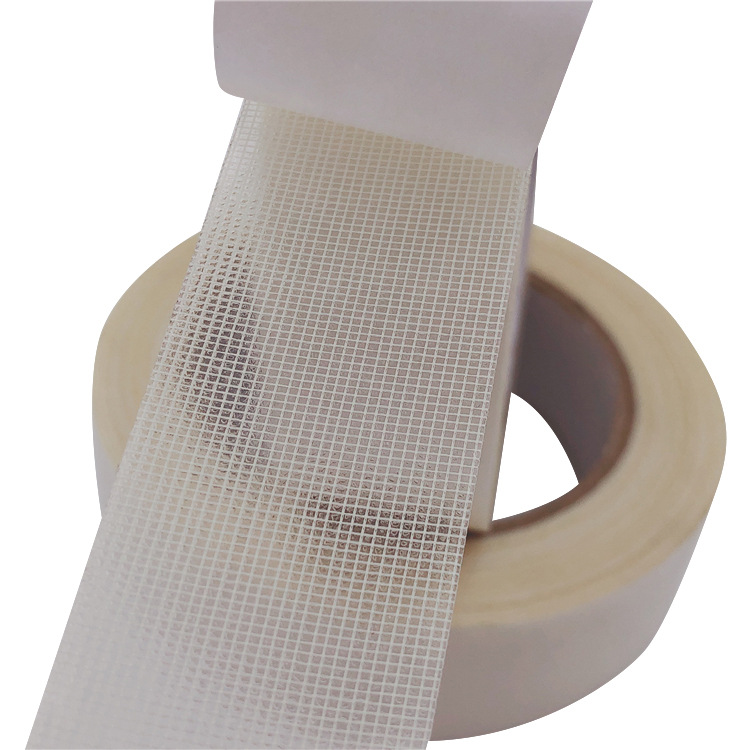
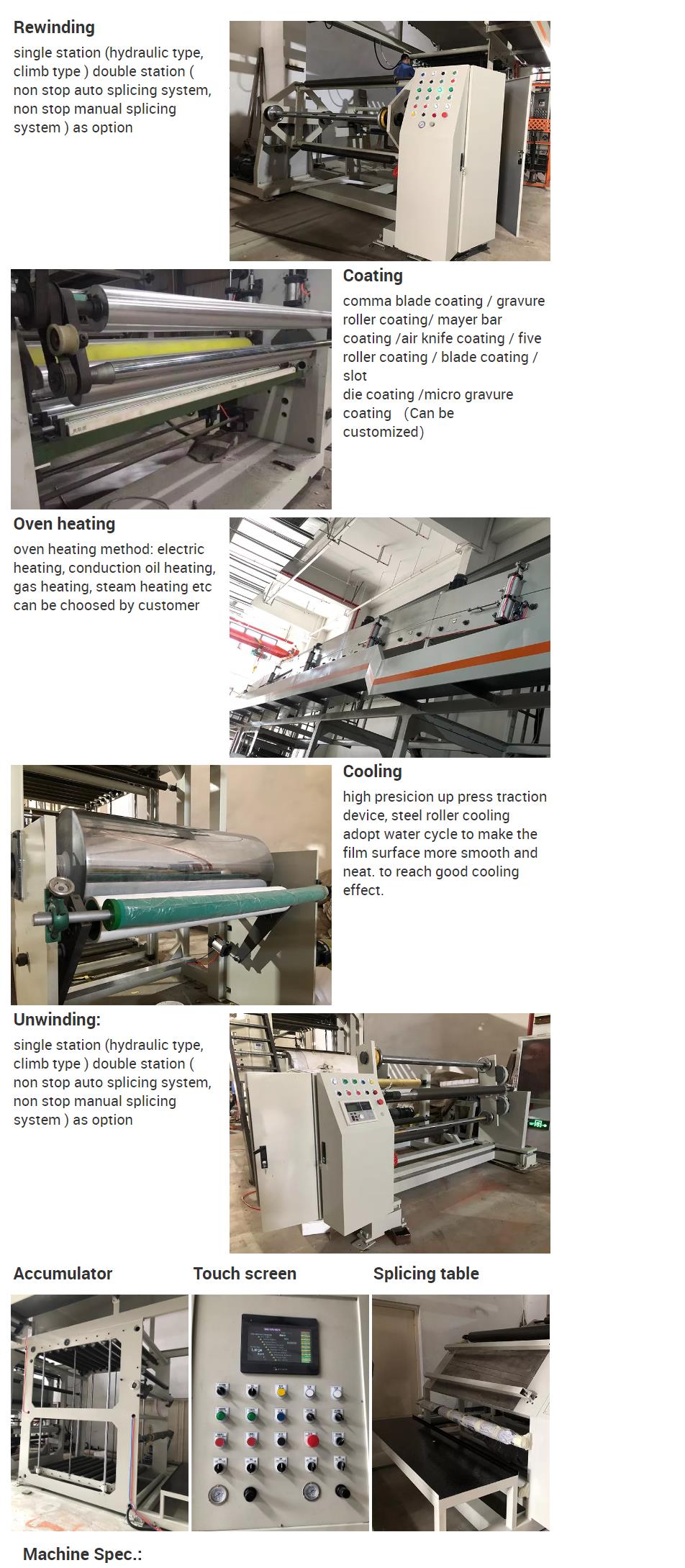
1. The whole machine is controlled by 7 frequency conversion motor. The tension of the whole machine (unwinding, coating, traction and winding) is automatically controlled by Western door PLC system. The reliability of the tension of the whole machine is improved through human-machine interface touch screen control and display.
2. The discharge rack is in the form of electric turnover double station and adopts magnetic powder automatic tension control.
3. (primer) anilox coating mode: the coating scraper shaft adopts heavy-duty double shaft mechanical independent swimming. The scraper adjustment mode is manual with pneumatic, and the angle can be adjusted arbitrarily. The coating amount depends on the mesh line of the anilox roller. The anilox roller with different mesh line can be changed for different coating amount.
4. (surface coating) the clutch of comma scraper roll is pneumatically executed, the gap adjustment is controlled by micro adjustment devices of left and right gearbox, and the thickness of glue is measured by feeler gauge.
5. The drying oven adopts 9-meter independent air inlet and exhaust, which can be heated by 9-meter independent air inlet and exhaust system, and can be divided into 3-meter heating and drying section.
6. The guide wheel in the oven is actively synchronized with the host, and the transmission adopts synchronous belt wheel transmission to reduce material tension and deformation. The air cylinder open top oven and membrane piercing operation platform make it easy for operators to work.
7. The intermediate tension of coating roller - traction steel roller is synchronized with floating swing arm type, which is automatically controlled by PLC
8. Automatic meter speed control device
9. EPC ultrasonic edge alignment machine is used for deviation correction, so as to ensure the tidiness of material winding.
10. Key type inflatable shaft is adopted for retraction and release, equipped with safety collet, so as to facilitate loading and unloading operation.
11. High precision up pressure traction device, water circulation type is adopted for steel roll cooling, and the film is smoother, more scraped and more cooling effect is achieved through the cooling roll.
12. The material receiving rack is in the form of electric turnover double station. The winding adopts double frequency conversion motor, and the vector frequency converter is controlled by PLC computer system.
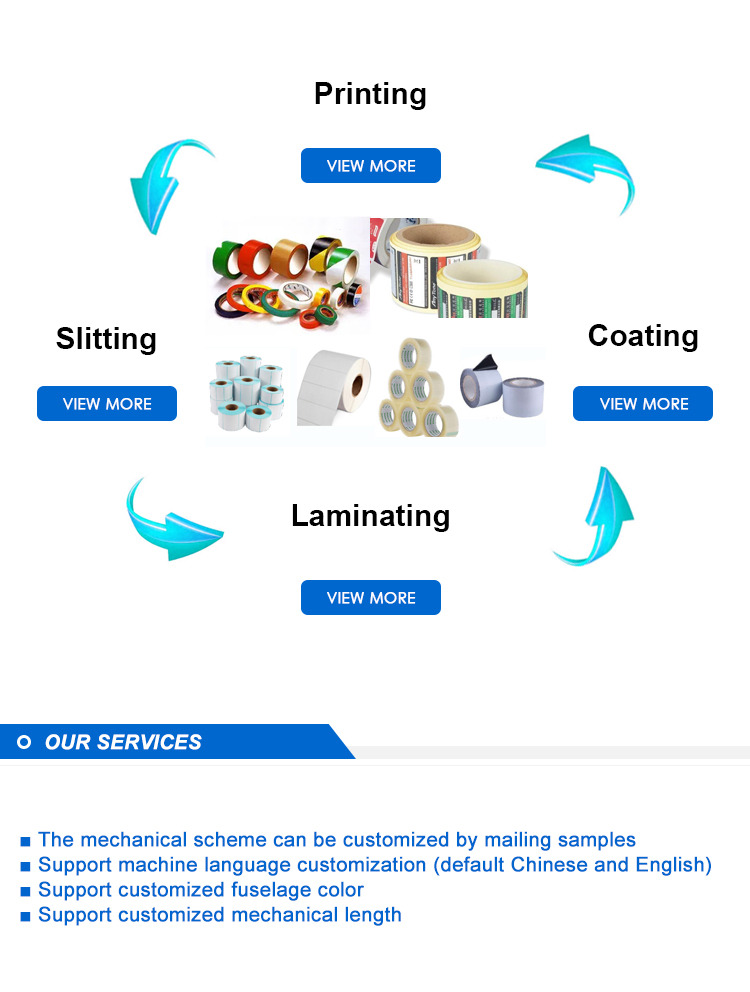
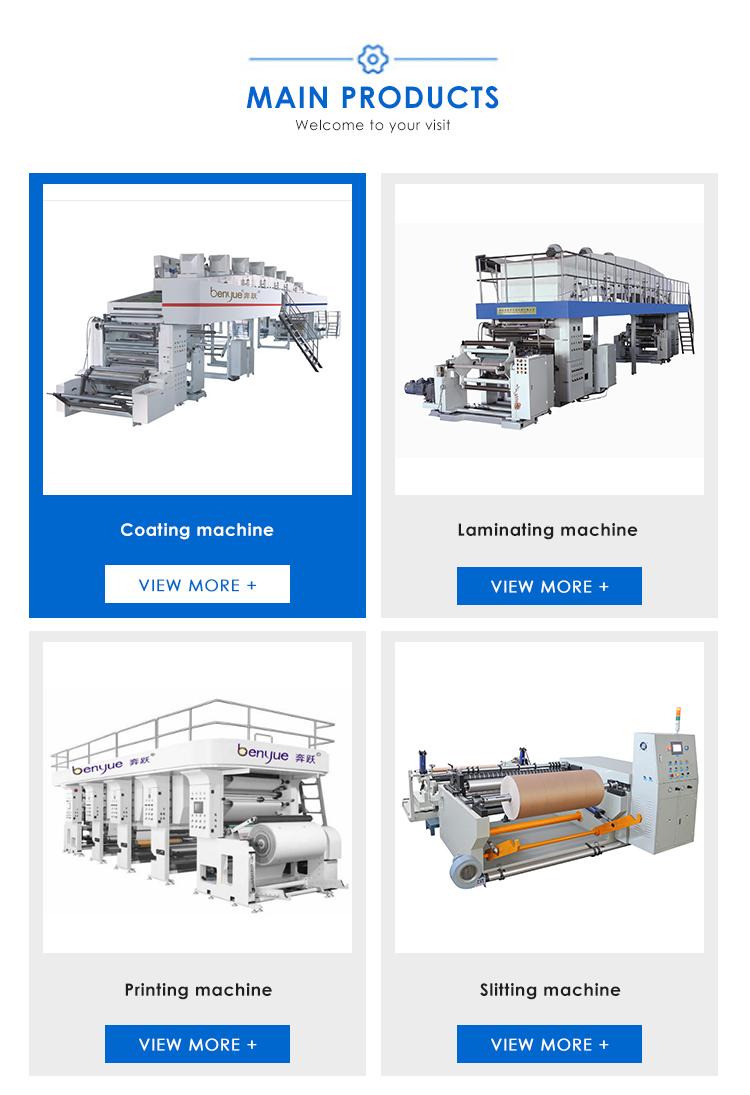
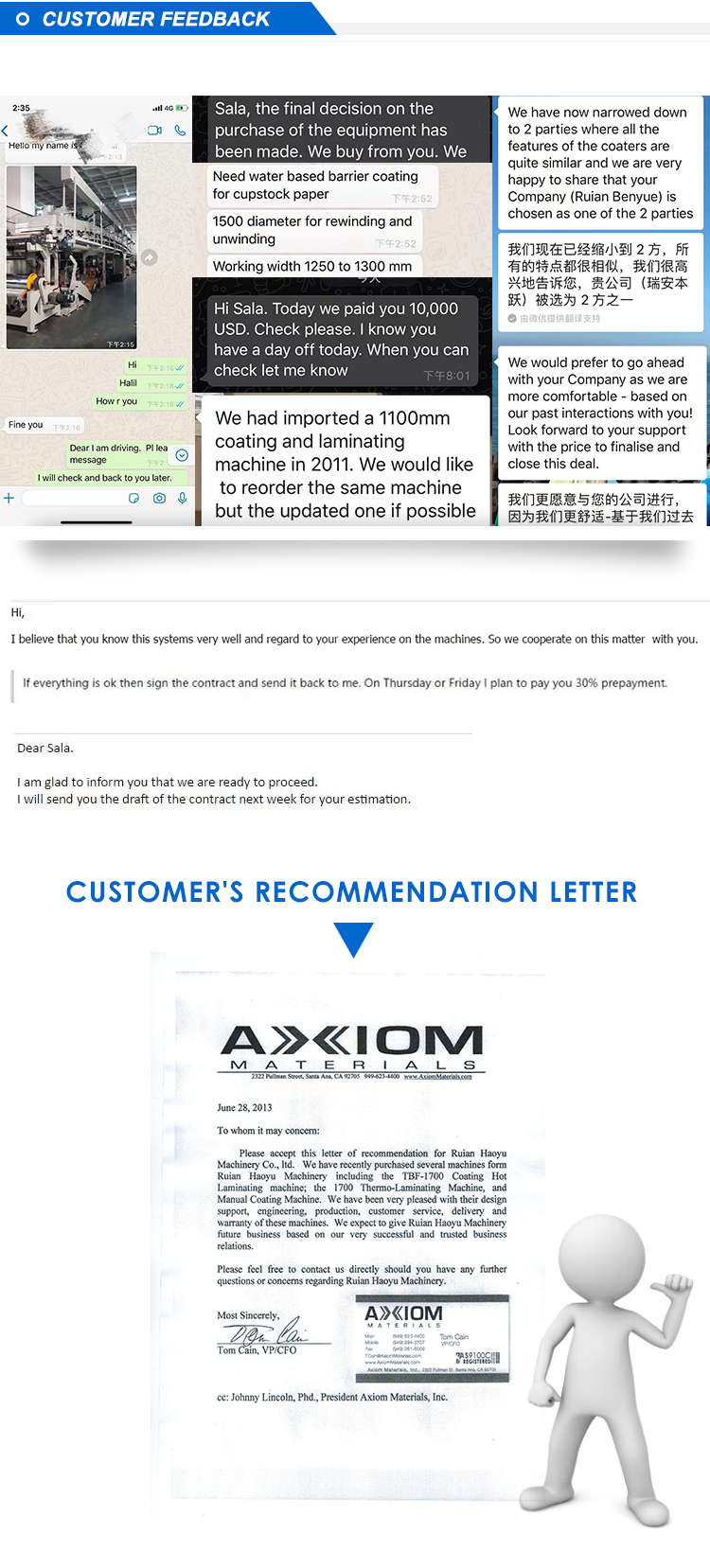
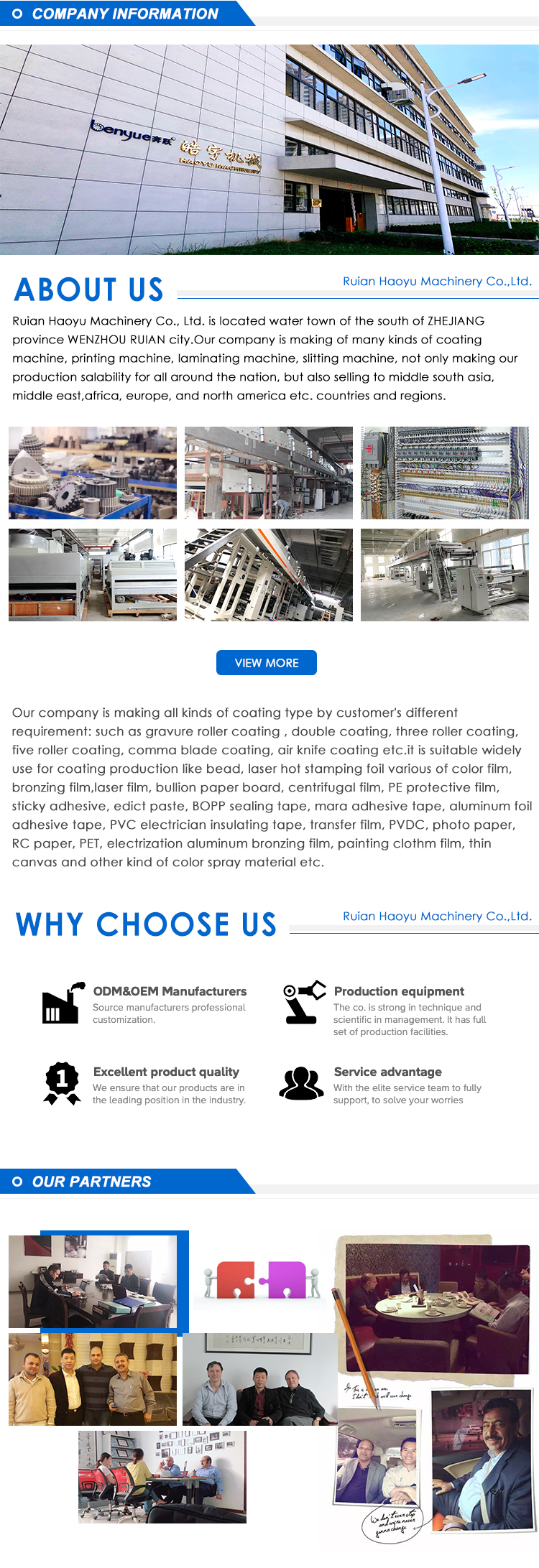
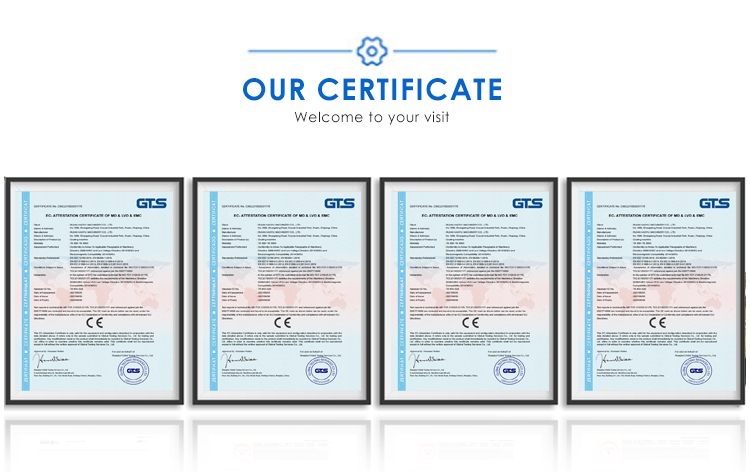
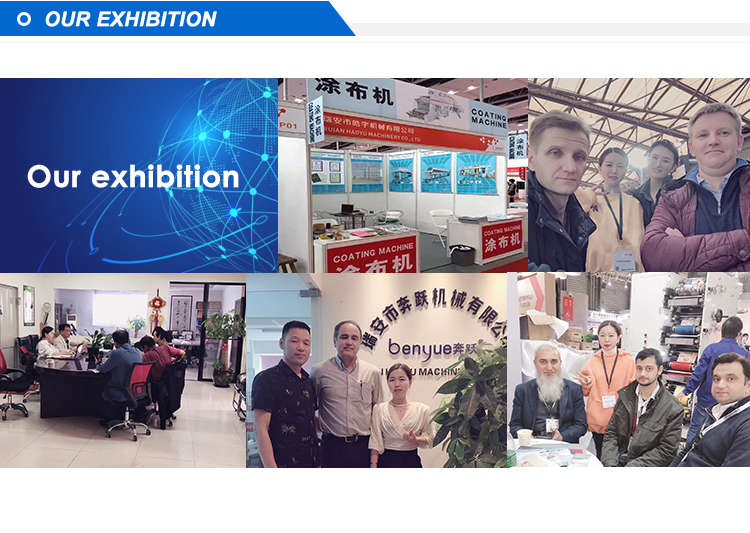
